Machine tool processing is widely applied in fields such as mechanical manufacturing, automotive manufacturing, and aerospace. With the implementation of policies promoting large-scale equipment upgrades, the machine tool and cutting tool industry may already be on the path to recovery.
During metalworking processes involving turning, milling, drilling, and grinding, high-speed and ultra-high-speed CNC machines generate substantial amounts of cutting heat during operation. The cutting fluid used for lubrication and cooling readily evaporates under these conditions, resulting in the formation of copious oil mist particles in the air. These oil mists typically contain chemical substances like dimer acids, polybutene, and colorants, which upon decomposition can produce toxic components such as styrene aldehyde, benzopyrene, and polychlorinated biphenyls (PCBs), posing a health hazard to workshop personnel. Suspended in the workshop atmosphere and adhering to the outer surfaces of machine tools and heat exchangers, oil mists increase thermal resistance, shorten equipment service life, and over time lead to malfunctions in the electrical systems and circuitry of the machinery.
To mitigate the pollution and hazards caused by oil mists, protect the safety and health of workshop workers, enhance workshop air quality, and prolong equipment lifespan, there is an urgent need to purify and recover industrial oil mists. Selecting appropriate oil mist purification devices has become an inevitable choice for ensuring safe production, energy conservation, and green production within the mechanical processing industry.
How Mechanical Oil Mist Purifier works
Industrial Mechanical Oil Mist Purifiers are highly effective equipment for addressing machining-generated oil mist. They employ coalescence filtration principles, where oil mist, under the suction of a fan, passes through a filter core. Fine particles are captured by fibers, migrating along the fibers and coalescing into larger droplets. These larger droplets, under the influence of gravity, drain out of the filter layer, thus achieving oil mist filtration and purification.
The MEGAUNITY Mechanical Oil Mist Purifier is suitable for various machining industries.
• The MEGAUNITY Mechanical Oil Mist Purifier utilizes a composite glass fiber filter core, capable of handling medium to low air volume and moderate particulate concentration scenarios, offering excellent cost-effectiveness and versatile adaptability.
• The equipment comprises a modular filtering system with an integrated fan, allowing users to select the number of filtration stages according to the level of contamination in the incoming air and the required outlet emission standards.
• Low-concentration mechanical oil mist purifiers can be equipped with either two or three-stage filters, suitable for applications involving grinding machines, lathes, milling machines, and other machine tools that utilize water-based cutting fluids or low-concentration cutting oils.
• High-concentration mechanical oil mist purifiers can be fitted with a four-stage filter assembly.
Multi-stage filtration offers high purification efficiency.
• 1st-stage filtration employs a stainless steel wire mesh, capable of capturing the majority of water mist and dust particles larger than 1μm, effectively protecting downstream filters, and is reusable after thorough cleaning.
• 2nd-stage filtration uses MEGAUNITY-modified coarse glass fiber filter media, featuring low operating resistance, high oil holding capacity, and extended service life. It can filter approximately 60% of oil mist and dust particles, with the reclaimed cutting fluid being recyclable.
• 3rd-stage filtration utilizes MEGAUNITY-modified self-cleaning medium-efficiency glass fiber filter media, demonstrating good oil drainage performance. Following the first two stages, it achieves a filtration efficiency >95% for particles with a diameter of 0.3μm, with the cutting fluid also being recyclable.
• The 4th-stage filtration incorporates H13-grade high-efficiency filter cartridges, designed to trap particles smaller than 0.3μm, offering high purification efficiency, lightweight construction, ease of installation, and allowing direct discharge into the workshop after purification.
Following the four-stage filtration process, the purification efficiency for pollutants smaller than 0.3μm exceeds 99.9%.
MEGAUNITY Mechanical Oil Mist Purification System Application Case
Heavy Industry Wheel Production Line Cutting Fluid Aerosol Control Project
Project Overview:
The workshop currently houses 12 CNC machining centers utilizing water-soluble cutting fluids, operating continuously for 24 hours a day. During the wheel manufacturing process, these machines generate a substantial amount of aerosol. To improve the production environment, ensure employee safety, enhance workforce efficiency, and extend equipment lifespan, it is necessary to collect and treat the aerosol generated during production processes before discharging it within the workshop, meeting relevant emission standards.
MEGAUNITY Solution:
MEGAUNITY, considering the specific site conditions, designed and implemented a Mechanical Oil Mist Purification System solution for the client.
For this project, a total of 12 machines requiring treatment were divided into 6 oil mist purification systems, with a cumulative designed air volume exceeding 48,000 m³/h.
Each individual machine was allocated a design air volume of ≥4,000 m³/h, with every pair of machines connected to a single Mechanical Oil Mist Purifier with a capacity of >8,000 m³/h for purification purposes.
The Mechanical Oil Mist Purifier employs a multi-stage filtration approach. Air is drawn in through the lower intake of the filter, sequentially passing through stainless steel wire mesh filters, primary P-type cartridges, intermediate S-type cartridges, and activated carbon filters before being discharged in compliance with emission standards.
Treatment Effectiveness:
Purification Efficiency: After treatment, the aerosol concentration from the machining centers is reduced to ≤1 mg/m³, with an overall system purification efficiency exceeding 98%.
Air Duct Velocity: The velocity within both branch and main ducts is consistently maintained within the range of 10-16 m/s.
Odor: The intensity of irritating odors at the production site is significantly reduced.
Noise: The overall noise level of the main unit is ≤75 dB.
MEGAUNITY is capable of providing tailored oil mist treatment system designs for various machining scenarios, encompassing the supply, transportation, installation, and commissioning of electrical components, equipment, piping, and all essential main units, accessories, and auxiliary materials. By offering turnkey engineering services, MEGAUNITY ensures that the systems operate more stably, affording users greater peace of mind.
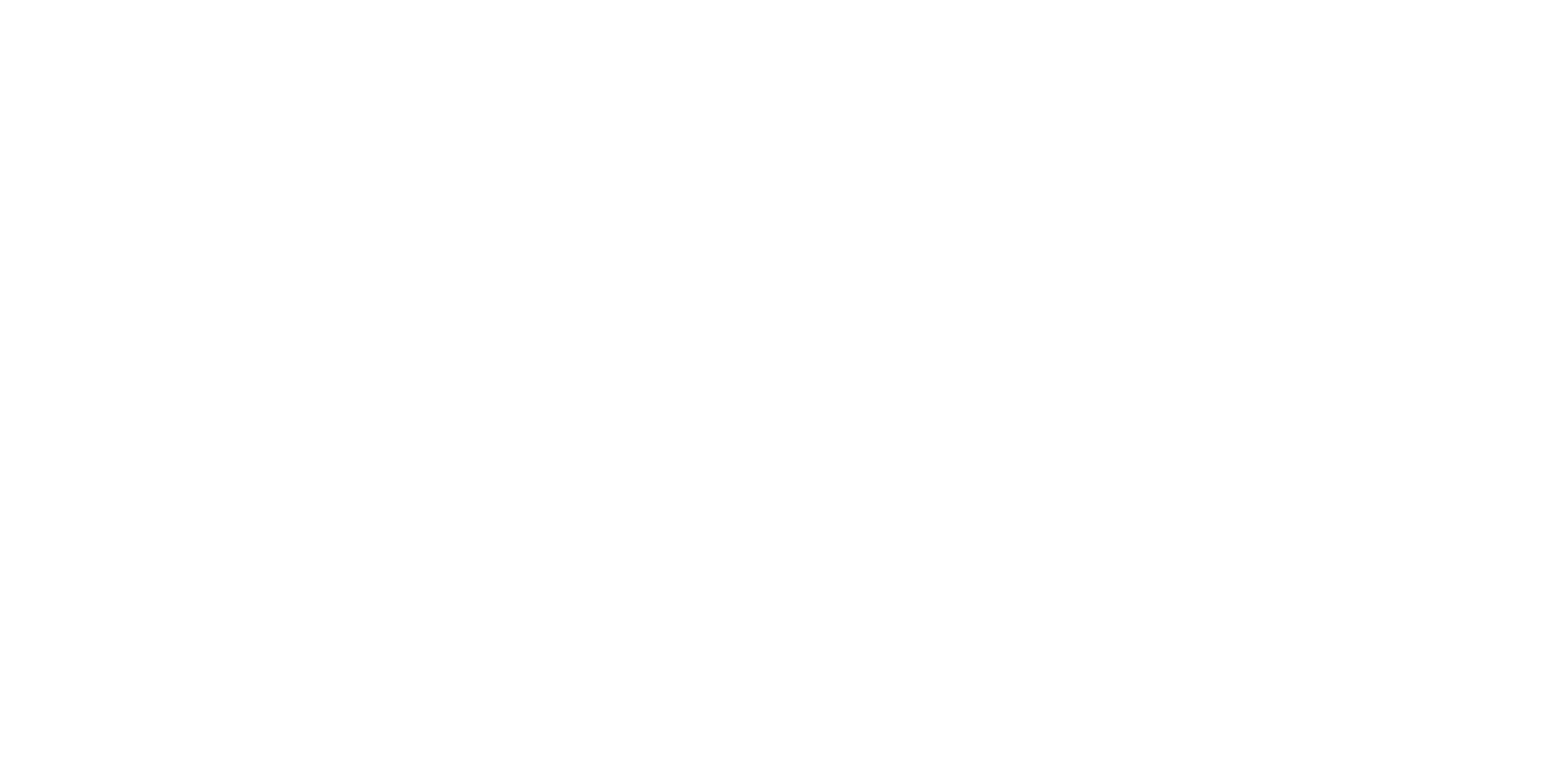
Industrial Air Handling System Solutions Provider
Tel:400-860-5288
E-mail: marketing@megaunity.com
Address:
No.300, Dongxin Road, Wuzhong District, Suzhou, Jiangsu, China
No.8, Shuzi 3rd Road, DD Port, Dalian Jinpu New Area, Liaoning, China
Copyright © 2022 Megaunity Air System Co., Ltd. All RIght Servered